Solid Carbide roughing End Mill
Features
1. High material removal rate: Tungsten carbide roughing end mills are designed with fewer flutes compared to standard end mills. This allows for larger chip load and more aggressive cutting action, resulting in higher material removal rates. They are ideal for quickly removing large amounts of material in roughing operations.
2. High hardness and wear resistance: Tungsten carbide is known for its exceptional hardness and resistance to wear. This makes roughing end mills made from tungsten carbide highly durable, even when machining hard materials like stainless steel, alloy steel, or cast iron.
3. Coarse tooth design: Roughing end mills usually feature larger and more widely spaced cutting teeth compared to other end mills. This design helps to achieve efficient chip evacuation and prevents chip clogging, ensuring smooth cutting operations.
4. Chip breakers: Some tungsten carbide roughing end mills may have chip breakers or chip splitters on the cutting edges. These features help to break long chips into smaller, more manageable pieces, promoting better chip evacuation and reducing the risk of workpiece damage.
5. High heat resistance: The high-temperature resistance of tungsten carbide allows roughing end mills to withstand the heat generated during heavy material removal. This heat resistance helps to prevent tool deformation or premature tool failure, ensuring longer tool life.
6. Variable helix or variable pitch design: Some roughing end mills have a variable helix or variable pitch design on their flutes. This feature helps to reduce chatter and vibration during the cutting process, resulting in improved surface finish and increased tool stability.
7. Coating options: Roughing end mills can be coated with various coatings, such as TiAlN, TiCN, or AlTiN. These coatings enhance the tool's performance by reducing friction, increasing chip flow, and improving wear resistance. The right coating selection depends on the specific application and workpiece material.
8. Robust construction: Tungsten carbide roughing end mills are built with a sturdy and durable construction to withstand the demands of roughing operations. They are designed to handle high cutting forces and provide stability during heavy material removal.
9. Shank options: Tungsten carbide roughing end mills are available with various shank options, including straight shanks, Weldon shanks, or Morse taper shanks. The shank choice depends on the machine's tool holder and the specific requirements of the machining setup.
10. Tool geometries: Roughing end mills can have specific tool geometries to optimize the cutting performance. These geometries may include increased core diameter, reinforced corner radii, or special edge preparations to enhance tool strength and performance during roughing operations.
Detail display
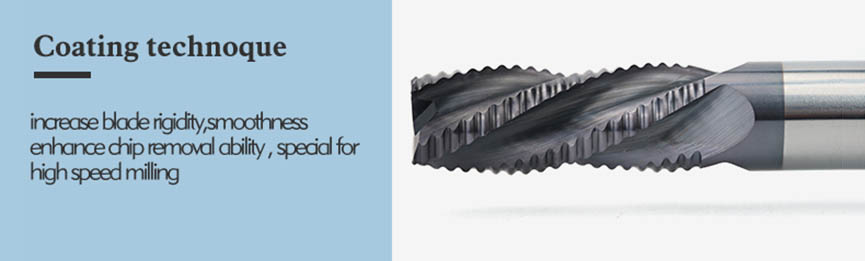
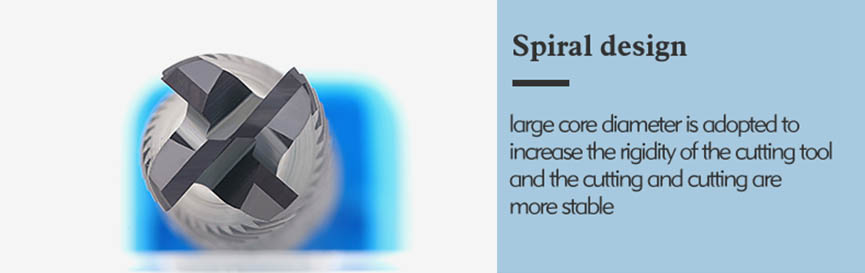
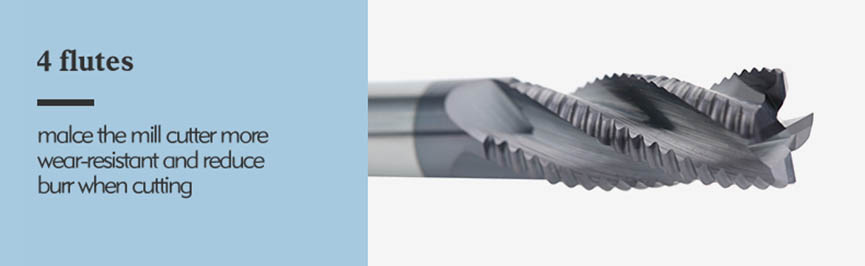
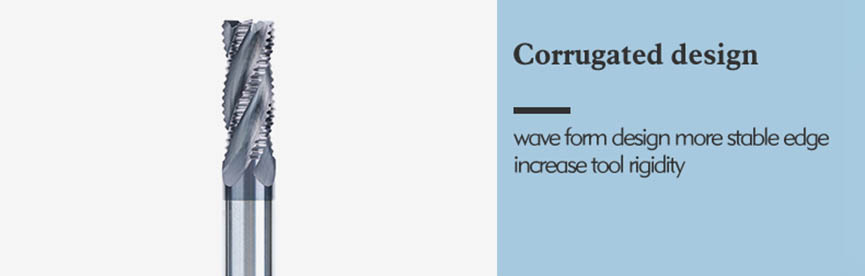
FACTORY
